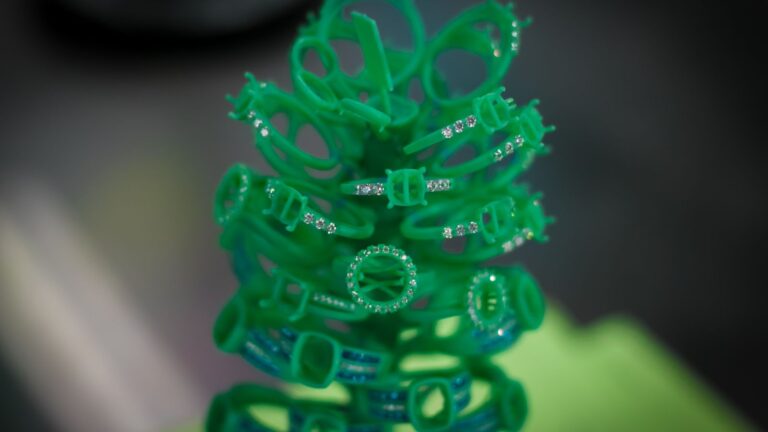
Introduction
Discover the ancient art of lost wax casting and unlock your potential for creating exquisite custom jewelry pieces that are truly one-of-a-kind. Not only is this time-tested technique ideal for capturing intricate details, but it also allows artists to unleash their creativity with endless design possibilities.
From selecting the perfect wax to mastering carving techniques and casting process, our comprehensive guide will equip you with everything you need to turn your jewelry making dreams into reality.
Key Takeaways
- Lost Wax Casting Jewelry is a time-honored jewelry-making technique that allows for intricate detailing and endless design possibilities.
- The lost wax casting process involves creating detailed wax models, building molds around them using investment powder, burning out the wax to create an empty cavity, and pouring in molten metal to create the final piece of jewelry.
- Essential tools for successful lost wax casting include carving knives, files, sprue cutters, crucibles and melting equipment. Choosing the right type of wax is also crucial to achieving desired outcomes.
- Mastering lost wax casting requires patience, attention to detail and proper protective gear. With practice and experimentation with materials like microcrystalline or natural beeswax anyone can achieve stunning results while making their own unique pieces of wearable art.
Understanding The Lost Wax Casting Process
The lost wax casting process involves creating a mold or pattern using a special type of wax, which is then coated in plaster and heated to create a hard mold that can withstand high temperatures.
Definition And Technique
Lost wax casting, a centuries-old technique also known as “investment casting” or “cire perdue,” is an intricate process used to create stunning and unique jewelry pieces.
The method involves creating a detailed wax model of the desired design, which is then encased in heat-resistant molds made from investment powder.
This versatile technique allows for high level of detail in jewelry designs and can capture even the most intricate patterns and textures. For example, artists inspired by nature may use lost wax casting to create woodland-themed creations with lifelike leaves and twigs seamlessly incorporated into their work.
Additionally, metal alloys such as gold, silver or bronze are commonly used to cast these unique pieces – adding durability while maintaining exquisite craftsmanship.
Materials Used
Lost wax casting requires the use of specific materials to create stunning jewelry pieces. These include various types of high-quality waxes, such as microcrystalline and natural beeswax, depending on the desired outcome.
Investment powder is also necessary for creating a mold around the wax model. Various metal alloys are used in lost wax casting, including bronze, gold, silver and brass.
Crucibles and melting equipment are necessary to melt the alloys into liquid form before pouring them into the molds during casting.
For off-grid living enthusiasts interested in this technique, knowing which materials to procure ahead of time will help ensure a successful project outcome.
Tools Necessary For The Process
To successfully execute the lost wax casting process, you’ll need several tools and materials. First and foremost, you’ll require a carving tool to shape the wax into your desired design or texture.
A sprue cutter is also necessary for cutting channels that will let molten metal flow through the mold. For melting and pouring the metal, a crucible and investment powder are needed.
The investment powder is mixed with water to form a solid shell around your wax model before it’s put in an oven to burn out the wax and leave behind an empty cavity for pouring melted metal in its place.
Lastly, polishing tools such as buffing wheels are used to give your finished jewelry piece a smooth surface finish.
Advantages Of Lost Wax Casting For Jewelry Making
Lost wax casting offers numerous advantages for jewelry making. It allows artists to create intricate and detailed designs, something that would be difficult using traditional methods.
Jewelry created through lost wax casting can also be incredibly unique, as each piece is handcrafted and one-of-a-kind. Additionally, the process enables artists to experiment with different materials such as bronze, gold, silver, or brass alloys which adds a level of customization beyond what is available with mass-produced jewelry.
Another advantage of lost wax casting is its ability to produce precise replicas of an original design without losing any details in the reproduction process.
Wax Carving Techniques For Jewelry Making
Learn how to choose the right wax, use carving tools, create intricate designs and textures, and prepare the wax for casting with our comprehensive guide on wax carving techniques for stunning jewelry making.
Choosing The Right Wax
Choosing the right wax is crucial to creating successful lost wax castings. When selecting a wax, it’s important to consider its melting properties and how well it can capture fine details.
Some popular waxes used for jewelry making include natural waxes, like beeswax or carnauba wax, as well as synthetic waxes, such as microcrystalline or sculpting waxes. Natural waxes are preferred by some artisans because they are easy to carve and have a low melting point.
However, synthetic waxes tend to be more durable and offer better control over details due to their higher plasticity.
Using Tools For Carving
To bring your jewelry designs to life, you’ll need to be able to carve intricate details into wax models. Essential tools for carving include wax carving knives, files, and other shaping tools.
A dental pick is also useful for making fine lines and textures in the wax. To create raised elements or add texture, a heated metal tool known as a “burnisher” can be used to smooth the surface of the wax model.
Choosing the right tools will help you achieve precise cuts and curves that will translate seamlessly into your final piece of jewelry.
Creating Intricate Designs And Textures

One of the most exciting aspects of lost wax casting is the ability to create intricate designs and textures in jewelry. Wax carving allows for incredible detail, with tools like micro carving tools or dental picks used to add texture and depth to the model.
The choice of wax is also key, as different types have varying degrees of hardness and workability.
Once the wax model has been completed, it’s time for sprueing – attaching channels that allow molten metal to flow through the mold. This stage requires careful planning and precision, as any flaws could lead to an unsuccessful cast.
For example, adding too many sprues can cause turbulence in the liquid metal that affects its quality. Similarly, too few sprues might not provide enough pathways for molten metal flow resulting in voids or imperfections within castings during solidification process which is best avoided by experienced professionals who have done this before using tried-and-tested methods.
Preparing The Wax For Casting
Once the wax carving is complete, the next step in lost wax casting for jewelry making involves preparing the wax for casting. The wax mold needs to be sprued and attached to a casting button or base.
Spruing allows any trapped air and gases inside the mold to escape during heating and pouring of metal, which helps ensure that the finished piece will not have any defects or holes.
Before moving on to investment casting, it’s important to inspect the wax model carefully for any cracks or deformities that can ruin the final product. To avoid such issues, some professionals prefer coating their models with a thin layer of heat-resistant material that ensures consistency and uniformity during heating.
The Investment Casting Process For Jewelry Making
The investment casting process for jewelry making involves building a mold, burning out the wax, pouring in the metal, and finishing techniques.
Building A Mold
Building a mold is an important part of the lost wax casting process for jewelry making. The first step in this stage involves creating a “sprue,” which is basically a channel that allows the melted metal to flow into the mold.
Once the sprue has been created, it’s time to build up layers of plaster around the wax model until it’s completely covered and encased in what’s called “investment.” Investment powder typically contains gypsum, silica, and other materials that help ensure a smooth and even surface for casting.
After several hours or days have passed (depending on the size of the mold), temperatures are raised slowly to melt out any remaining wax from within investment material.
Overall, building a mold requires attention to detail in order to get accurate and intricate results; correct sizing of channels becomes especially crucial since misalignments can result in defects or weaker parts down along with poor finishes depending on luck factors such as temperature control during pouring processes.
Burnout Process
Once the wax model has been created, it undergoes a burnout process to remove any remaining wax and prepare the mold for casting. During this process, the mold is heated slowly to a high temperature until all the wax is melted and burned out of the cavity.
This creates an empty space or negative impression where molten metal can be poured to create the final jewelry piece. The burnout process requires careful control of temperature and time, as well as proper ventilation to prevent toxic fumes from contaminating your living space.
It’s important to use appropriate protective gear such as gloves, masks, and goggles when handling hot molds or working with foundry equipment.
Pouring The Metal
After the burnout process, it’s time for pouring the metal. The melted metal is poured directly into the mold through a sprue hole using a centrifugal or vacuum casting machine.
The molten metal is then left to cool and solidify inside the plaster mold.
It’s important to choose your metals wisely when lost wax casting as they can affect not only the final quality of your piece but also pose safety concerns during melting and pouring.
Common metals used in lost wax casting include bronze, silver, gold, and brass alloys.
Finishing Techniques
After the metal has been poured into the mold, it’s time to remove any excess metal and polish the finished piece. This is where finishing techniques come in. Finishing techniques include filing, sanding, buffing, and polishing to create a smooth surface and shine that will enhance the beauty of your jewelry piece.
In addition to polishing tools such as rotary tools with various attachments for grinding, sanding pads or files can be used to shape or smooth rough areas on a cast item.
Also, tumbling machines can be used for mass-production or high-quality items- which use abrasive media along with water and soap solution to give necessary luster while removing any sharp edges resulting from casting process.
Overall, mastering lost wax casting involves understanding various aspects like preparing molds properly choosing materials wisely and most importantly creating intricate designs through wax carving which accurately portrays your desired shapes before it passes through melting temperature hence creating beautiful and unique jewelry pieces worth showcasing!
Essential Materials And Equipment For Lost Wax Casting
To master the art of lost wax casting and create stunning jewelry, it is essential to have the right materials and equipment including investment powder, metal alloys, crucibles, melting equipment, casting machines, polishing tools, and more.
Wax
One of the most critical components in lost wax casting is wax. When using this technique, choosing the right type of wax to cast your jewelry design is crucial. Different types of waxes are available for different needs, including carving and injection waxes, each with its unique properties that can significantly impact the final result.
Carving waxes are firm and ideal for creating intricate designs and textures by hand-carving or using cutting tools.
It’s essential to ensure that your chosen wax has consistent melting properties to prevent deformation during casting. Temperature control is also vital when handling melted wax as it can ignite easily at high temperatures.
Investment Powder
Investment powder is a key component in the lost wax casting process for making stunning jewelry creations. Also known as casting plaster or investment mold, this special mixture of silica, gypsum, and other minerals creates a hard shell around the wax model that will later hold molten metal during casting.
To prepare this mixture for use, it’s important to follow specific instructions on water-to-powder ratios and mixing times to ensure a smooth consistency without any lumps or air bubbles.
Using investment powder can be a messy process, but with proper equipment like rubber gloves and face masks, safety measures can be taken to make it an enjoyable experience.
It is important to note that once invested (placed) into the mix, it must fully dry before jewelry can be casted using lost-wax techniques.
Metal Alloys
Metal alloys play a critical role in lost wax casting for jewelry making. These materials are formed by combining two or more metals to create a new material with unique properties and characteristics.
Alloys allow jewelers to vary the color, strength, and texture of their creations depending on their desired outcome.
Different metal alloys also have varying melting points which can affect the casting process. Some common alloys used in jewelry making include brass, bronze, gold, and silver.
Brass is an alloy that contains copper and zinc and is commonly used for intricate designs due to its malleability. Bronze, on the other hand, is made from a mixture of copper with tin or aluminum that produces strong castings ideal for large pieces like sculptures.
Crucibles And Melting Equipment
To successfully create stunning jewelry creations using the lost wax casting technique, it is essential to have high-quality crucibles and melting equipment. Crucibles are containers used for melting metal, while melting equipment includes tools such as torches and furnaces that are used to heat the metal until it is in a liquid state.
For those living off-grid, there are many options available when it comes to choosing crucibles and melting equipment. Some choose to use propane or wood-fired furnaces which can be easily built from scratch with locally-sourced materials.
Whatever method one uses, though, it’s important to ensure that all safety precautions are taken during the melting process – this includes wearing protective gear such as glasses or a face shield and working on surfaces that will not ignite when exposed to heat.
Casting Machines
To produce high-quality cast metal objects, you’ll need to use a casting machine. These machines help guarantee consistent results by allowing you to control the temperature and speed of the melting process.
Centrifugal casting uses a centrifuge to create precise pressure gradients that force molten metal into molds. Vacuum casting involves removing air from the mold cavity before adding liquid metal, which helps ensure extremely detailed surfaces on your final piece.
Polishing Tools And Equipment
Once the metal has been successfully cast, it’s time to polish it to perfection. There are several tools and equipment required for this step, including a polishing machine and various buffing wheels made of different materials such as muslin, felt or sisal.
Polishing compounds like rouge or tripoli can be applied to the wheel to achieve specific finishes.
It’s worth noting that while there are many professional-grade machines available on the market, those living off-grid may need more creative solutions. For example, an old sewing machine motor can be repurposed into a motorized buffer by attaching V-belts to the pulley system.
Tips And Techniques For Successful Lost Wax Casting
To achieve successful lost wax casting, it is important to properly prepare the mold and select the right type of metal for your project. Maintain precise temperature control during the process and ensure proper safety precautions are taken when dealing with molten metal.
Mold Preparation
Mold preparation is an essential step in lost wax casting for stunning jewelry creations. Before pouring the metal, creating a mold that captures every detail of the wax model takes precision and care.
To begin, the prepared wax model is attached to a wax sprue, which will allow for molten metal to flow into every crevice of the mold. This “tree” of waxes is then encased in investment powder or plaster mix, where it solidifies and creates a negative space around the wax model.
It’s crucial to consider several factors when preparing molds; one wrong step can ruin hours or even days of work. Temperature control during heating and cooling stages must be precise to prevent cracking or other imperfections on your finished product.
Additionally, selecting specific materials such as investment powders or plaster mixtures should be based on preferences for size, shape, texture and type of metal alloy being used in casting for desired outcomes.
Metal Selection
When choosing the metal for your lost wax casting jewelry creation, it’s important to consider both aesthetic and practical factors. Metals like bronze, gold, silver, and brass are popular options due to their durability and ductility.
Bronze is a great choice for creating unique patina finishes while gold offers timeless elegance.
It’s also important to consider the properties of each metal when selecting one for your project. For example, some metals may be better suited for certain styles or types of jewelry making techniques.
Additionally, some metals may require special care or polishing techniques to maintain their appearance over time.
Temperature Control And Safety Precautions
Temperature control is a crucial factor in lost wax casting to ensure that the metal flows smoothly and evenly during the pouring process. It is imperative to maintain consistent temperatures throughout the entire casting process, including heating the mold and melting the metal.
Wear protective gear such as gloves and goggles while pouring molten metal into molds or handling heated waxes. Ensure proper ventilation in your workspace by wearing an air respirator mask if necessary.
Always operate equipment according to manufacturer instructions, keeping all wiring away from water sources or flammable materials.
Wax Carving Techniques
To create intricate designs and textures in wax, it is important to choose the right type of wax for carving. Waxes with higher melting points are ideal for creating fine details and sharp edges.
Carving tools such as knives, files, and chisels can be used to shape the wax and create various textures.
Many jewelry makers prefer using sprue casting when carving their waxes as it allows them to connect multiple models onto one sprue tree before casting. This process makes it possible to create several pieces at once while maintaining each piece’s unique design and texture.
After completing the necessary carvings on the individual waxes, they are cleaned thoroughly before being secured onto a sprue attachment that connects them together like branches on a tree.
Finishing And Polishing Techniques
After the metal has been poured and cooled, the piece is then ready for finishing and polishing. The process involves cleaning off any remaining investment material from the surface of the metal.
This can be done using various techniques such as sandblasting, tumbling or electrolysis.
Polishing is achieved by rubbing abrasives onto the piece in successive stages until it becomes perfectly smooth and shiny. There are several types of polishes that can be used depending on your preference including rouge, tripoli or Zam compound.
Rouge is commonly used for gold while tripoli works better on silver items.
Conclusion
In conclusion, mastering the art of lost wax casting can provide endless opportunities for stunning jewelry creations. From carving intricate designs to pouring the metal and finishing techniques, every step is crucial in ensuring a successful outcome.
With the right materials, tools, and techniques, anyone can become an expert in this ancient form of jewelry making. For those interested in further resources, there are many online tutorials available as well as hands-on classes with experienced instructors.
FAQs:
1. What is lost wax casting and how is it used in jewelry making?
Lost wax casting is a technique that involves creating a mold by sculpting an object out of wax, covering it with plaster or another material, melting the wax away leaving behind an empty cavity, and then pouring molten metal into the cavity to create a finished product. This method allows for intricate details to be captured in metal, making it popular among jewelers.
2. What materials can be used for lost wax casting in jewelry making?
Metals commonly used include gold, silver, bronze, copper and platinum though other alloys could work as well depending upon preferences & needs of artist/manufacturer.
3. Can I perform lost wax casting at home or do I need special equipment?
While some jewelry makers might have the resources to cast their own designs from start-to-finish – Many people find success partnering up with professionals who have experience creating custom pieces using this process.. For those interested in trying on their own there are starter kits available but experienced craftsmen generally rely on specialized tools such as electric kilns or hydraulic presses needed for more complicated jobs.
4. What are some advantages of using lost-wax casting over other techniques?
Because this approach enables greater complexity than other methods (such as sand-casting) meaning finer detail can be achieved within each design while allowing artists control over potential imperfections which ultimately adds value when compared against similarly priced items made otherwise! Another advantage lies within customization options – Anything from size/color/materials can all be tailored according personal preference without losing quality due limitations imposed by less precise methods best saved simpler compositions like rings rather than bracelets or necklaces.”.